3D Printing Series - What's Behind Our #3DThursday Posts
- Takin Our Toys and Livin
- Mar 5, 2020
- 8 min read
Updated: Mar 10, 2020
Article #2 of 3: Filaments - Why So Many? What's the Purpose?
We've received many questions in regards to our 3D Thursday posts, everything from what kind of printer we use to where we come up with the ideas, concepts and designs. We've also had several questions about what types and brands of filament we use, and for what applications do we use each one. These are questions that we typically don't go into in our 3D Thursday posts since those are geared more towards the design and print itself, something we started on our Instagram and Facebook page when we started full-time RVing as something a little unique in the RV community.

This article, the second in the series, is all about 3D printer filament. There are many different kinds of filament you can use for 3D printing, but in general they are all a type of plastic. The principle is very basic. The extruder pushes the filament through the hot end (print head in layman terms) which in turn melts the filament as it's pushed out onto the print bed in .4mm widths (typically) following the design loaded into the printer. As the filament is exposed to the ambient temperatures it re-solidifies into a hard plastic. This is done layer by layer, with each layer being .15mm - .3mm each. To put that in perspective, a 1-inch tall print in medium resolution (.2mm layer height) would be 125 layers of print when finished. So when people wonder why even the smallest of 3D prints take so long to print, that's why!

So let's talk about the different types of filament and their purpose for existence. There are numerous different types, colors, styles, and not all are plastic like you might think! There are some with properties that allow them to change color, some are transparent, some contain wood, some that are actual metal, and many others. There are so many variations of filament that it would be impossible to cover them all in this article, so we're going to focus on the most common hobbyist/consumer-based filaments on the market and why you need to think about your final application for a 3D printed model before you print it to determine the best filament for the job.
PLA (Polylactic Acid)

The first, and most common filament type is called PLA which is made from corn starch, a renewable resource. As well, it requires less energy to produce compared to petroleum-based plastics which makes it one of the cheapest filament types on the market. But what makes it one of the most common (besides its price point) is that it produces no harmful fumes, a subtle (but sweet) aroma and has minimal warping properties. As well, PLA can be printed on 3D printers that do not have heated print beds which are far less expensive, making them more accessible to the general hobbyist as well as schools, though heated beds definitely help with print adhesion. PLA also melts, and subsequently prints at a relatively low temperature (175-200°C) which is suitable for less expensive printer hot ends.
PLA has a wide range of uses, both at the professional level as well as for hobbyists. PLA is often used for medical sutures, and surgically implanted pins and rods due to the fact that it breaks down in the human body over 6 months to 2 years depending on the size and density of the part. Other professional uses include candy wrappers, food containers, and prototypes for CNC metal parts, forms to create injection-molded parts. For the hobbyist, PLA is a great all-around filament for printing common household items.
The only time PLA becomes an issue is when an application is going to be exposed to heat, for example a car smartphone holder that will sit in a hot vehicle and potentially in direct sunlight for hours. PLA has a glass point of 140-150° Fahrenheit, a temperature reached frequently inside of vehicles on a hot summer day. At this temperature PLA will start to warp or bend, even with no force on it other than gravity. But don't fear, the next filament type is ideal for this type of situation!
ABS (Acrylonitrile Butadiene Styrene)

The second most common filament is ABS which I bet many of you have heard of due to its popularity for countless consumer products on the market. Those include such things as plastic auto parts, knife handles, toys (like LEGOS!), and numerous other common items. And if you've ever stepped on a LEGO barefoot you know EXACTLY how hard this plastic is!! ABS has a much higher glass point of ABS is also relatively inexpensive.
So why not print with ABS all the time instead of using PLA or any of the other filament types? For one, ABS is more challenging to print. Not only does it require a 3D printer with a heated bed, it requires one that can get the bed temperature up to about 100°C which is not something all 3D printers can do, and even if they can achieve that temp an enclosure around the entire print area may be required for them to maintain that temp. ABS also prints at a higher temperature than PLA, typically between 220-250°C and it emits fumes which can be irritating and/or harmful, so when printing with ABS the area must be well ventilated. Also noteworthy, ABS is petroleum-based and as such, is not bio-degradable like PLA. But the biggest downside of printing with ABS, even if your printer is fully capable of achieving the necessary temperatures and has an enclosure, is that ABS is very prone to warping. This type of plastic constricts more than others as it cools which can be problematic, especially with sharp edges and corners. It's always a good idea to round edges and corners on your design if ABS is the desired material to print with.
That said, ABS has a glass point of 105°C (or 221°F), the point at which it will start warping. It's the most resilient filament (of the common hobbyist/amateur used filaments) to UV and heat, so it's ideal for those outside or higher temp applications.
PETG (polyethylene terephthalate glycol-modified)

Of all the common filaments, PETG probably has the most interesting story on where it came from and why it's gaining such popularity. PETG is relatively new, but has become a very popular alternative to PLA and ABS over the past couple of years for 3D printing. But to fully understand PETG we must first talk about where it came from.
PETG was conceived from PET (polyethylene terephthalate), one of the most common plastics in the world, used for food containers and water bottles and is FDA approved for such, medical device packaging, toys, kitchen utensils, just to name a few. PET is a rigid plastic with high moisture resistance, much like PLA and can become brittle and easily breakable with overheating. It can also become hazy.
With the addition of glycol, PETG is a much easier plastic to work with. The added glycol makes PETG far less brittle that PET or PLA, is 100% recyclable, has higher temperature resistance, and is more flexible. It is also easier to print with as it has very low shrinkage which minimized the chance of warping. However, it retains the chemical and moisture resistance of PET. It has been said that PETG combines the best characteristics of PLA and ABS for 3D printing and injection-molding. While PETG is not as easy to print as PLA and does require some trial and error with your printer's extruder z-offset, filament flow rate, filament retraction speeds and distance, and print speeds it produces consistent results print after print once these settings are determined for your particular printer and brand of filament.
PETG has a glass point of 88°C (or 190°F) so it isn't quite as heat tolerant as ABS, but it's close, and high enough for most higher temperature applications such items in a car, in direct sunlight, etc. It does require printing at higher temperatures (220-245°C), but only requires 70-80° bed temperature for solid adhesion, without any need for an enclosure. The end result is a strong, heat resistant print that has a high quality finish. The only time that PETG is not a suitable filament choice is for items that will have prolonged exposure to UV rays, as they will degrade the strength of the print. But for most items, PETG is "the best of both worlds" as an alternative to PLA or ABS.
TPU (Thermoplastic PolyUrethane)
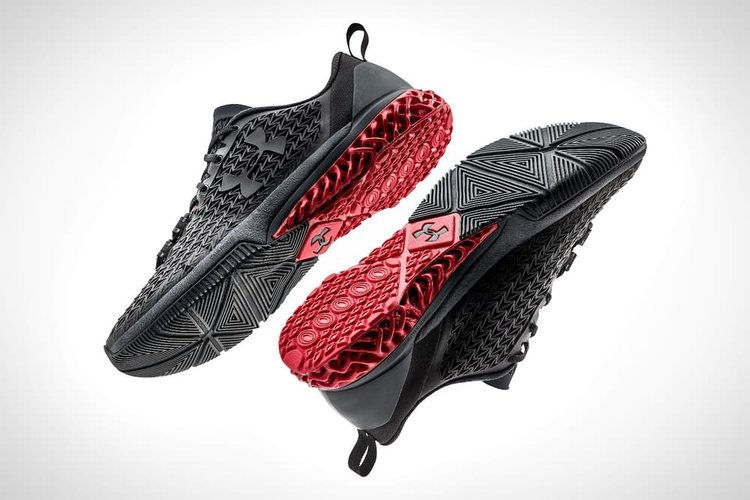
The last common filament that we'll cover in this article is TPU, a flexible filament that is ideal for "squishy" toys, rubber-like flexible phone cases, wearable items, sporting goods, door and window seals, shoe soles, and numerous other such things where a part needs to be pliable, have elasticity to it, and/or be impact resistant. You may see this filament referred to as TPE in the 3D printing world as they tend to be used synonymously; however, TPU is technically a type of TPE.
The key to printing TPU models that have the flexibility or stiffness you desire is actually determined more by the design and print settings (known as slicing) of the model. Sharp corners and edges are far less flexible that rounded sides and flat surfaces. Also, the thickness of the outer walls and the percentage of infill greatly affect the flexibility of the end product. The most flexible models will have thin outer walls and 0% infill, making them hollow.
TPU can be challenging to print with, but with some trial and error you can get to settings that print successful prints consistently. One key setting for successful prints is to turn filament retraction off for the entirety of the print. TPU prints at similar temperatures as ABS, from 210-225°C, but like PLA doesn't require a heated bed. It has minimal shrinkage and warping, and maintains a high quality finish resulting in a quality model print without significant post-printing cleanup. So if you need to print something that's flexible, TPU is the ideal filament choice.
Notable Mentions
These are the most common filaments used by the hobbyist and amateur 3D printing community, but there are many other types and variations of the types mentioned above. Without going into detail on all of them, there are a few that are worth calling out.

One of my favorite filaments is Wood. Wood filament is actually PLA, but has ~30% wood fibers and is ~70% PLA. These percentages vary by brand, but not by much. When you print with Wood filament it actually smells like wood. But my favorite part of using Wood filament is that fact that it is stainable, just like something actually made out of wood! It can also be painted, so this makes Wood filament ideal for a plethora of household items, decorations, etc.
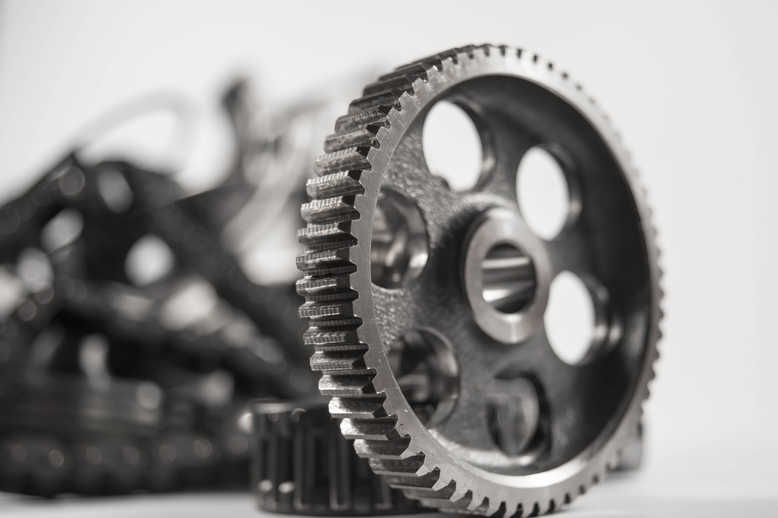

Another very unique filament is Metal. Like Wood, Metal filament is also a PLA with a percentage of metal powder or flakes in them. These Metal filaments
include copper, bronze, brass and stainless steel. The metal content of these PLA filaments make the printed models heavier that plain PLA and resulting prints looks like metal.
The last notable filament is Carbon Fiber. This filament can be purchased as PLA, ABS, PETG or TPU, but all include ~15% short strands of carbon fiber resulting in much lighter and

impact resistant prints. Carbon Fiber filament is ideal for printing drone or remote control
vehicle parts to achieve a stronger, yet lightweight part. As well, Carbon Fiber is great to use simply for aesthetics when you want that carbon fiber look.
Favorite Filament Brands by Type
Below are my favorite filament brands by type. I've tried many different brands, but these are the ones that I've had the most success with and/or had equal success with compared to more expensive brands.
PLA: Hatchbox and Overture - approximately $19-$24 per roll
ABS: Hatchbox - approximately $19-$24 per roll
PETG: Overture - approximately $22-$24 per roll
TPU: TronXY - approximately $23-$25 per roll
The one brand that is known for being a high-quality 3D filament that I have tried multiple times with both their PLA and ABS that never resulted in consistent, quality prints and were more challenging to print with, get decent bed adhesion, etc. was 3D Solutech. Your experience may be different. I know several people that swear by their filament, but I will never buy another roll of it; there are too many other quality options on the market to bother messing with theirs again.
Upcoming Article #3 - All About 3D Design and Printing Software
In the next post we'll dig into the types of software and some of the options for both 3D model design and 3D Slicing, the software that determines how the model is actually printed on the printer. We will also go through the basic process steps from design inception to completed print.
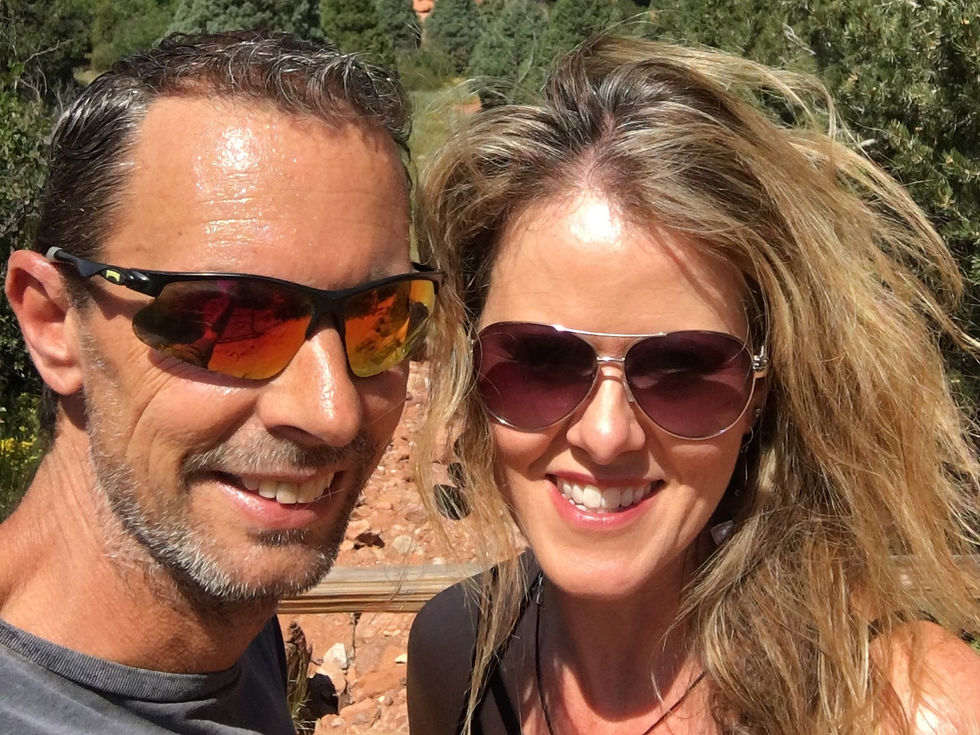
Please support our page by using our Amazon Affiliate link for any and all of your Amazon shopping needs!
Thanks, Dave! I didn’t go into a ton of detail on how to print with each filament, partially because every printer is a little different and settings vary based on type of hot end, print bed material, etc. The 3rd article will be all about design and slicing software, so you could probably write the Fusion360 section better than I can! 👍
Excellent article. Very informative. Looking forward to your next one. One day I will have a 3D printer and will put all this info to use!